Film Development & Scanning at Nice: A Complete Guide 2025
A step-by-step breakdown of what happens inside our NYC film lab.
Sending your film off can be one of the most nerve-wracking parts of being a film photographer. You’re trusting a lab with your memories, and it can feel unsettling when everything happens behind closed doors. That’s exactly why we’re writing this blog. At Nice Film Club, we believe you deserve more than just great scans—you deserve absolute peace of mind.
Over the years, we've built out a process that’s seamless, transparent, and designed with you in mind. From start to finish, your film is carefully tracked so nothing gets overlooked.
So, let us take you behind the scenes. You’ll see how we handle your film every step of the way, making sure the experience is as stress free and smooth as possible.
Creating an Account: Your Film Journey Starts Here
A key aspect of the Nice Film Club process is establishing track-ability at every stage. When you create an account, you are assigned a unique user ID—a series of numbers that serves as your personal identifier. This ID is linked to every order you place. Your user ID is visible to the lab technician across the entire process and is used to mark the folder where your negatives will be archived.
User ID_Order Number_Roll Number
Smooth, Simple, and Stress Free Film Drop-Off
Nice Film Club accepts film submissions both by mail and in person. Each time you place an order, you receive a unique order number via text and email. This number is different for every order you make and serves as the primary way for Nice to track your film.
For mailed in orders, the order number (the middle number in the series above) is used to locate your specific order on the Nice Film Club website, so it is helpful to write that number clearly on your package. When dropping off film in person, providing this order number to the lab technician helps them quickly find and process your order. It is the most effective way to guarantee a smooth intake process.
Once an order is received the lab tech will print the dedicated order sheet along with the twin checks and pair them with the roll(s) inside a folder.
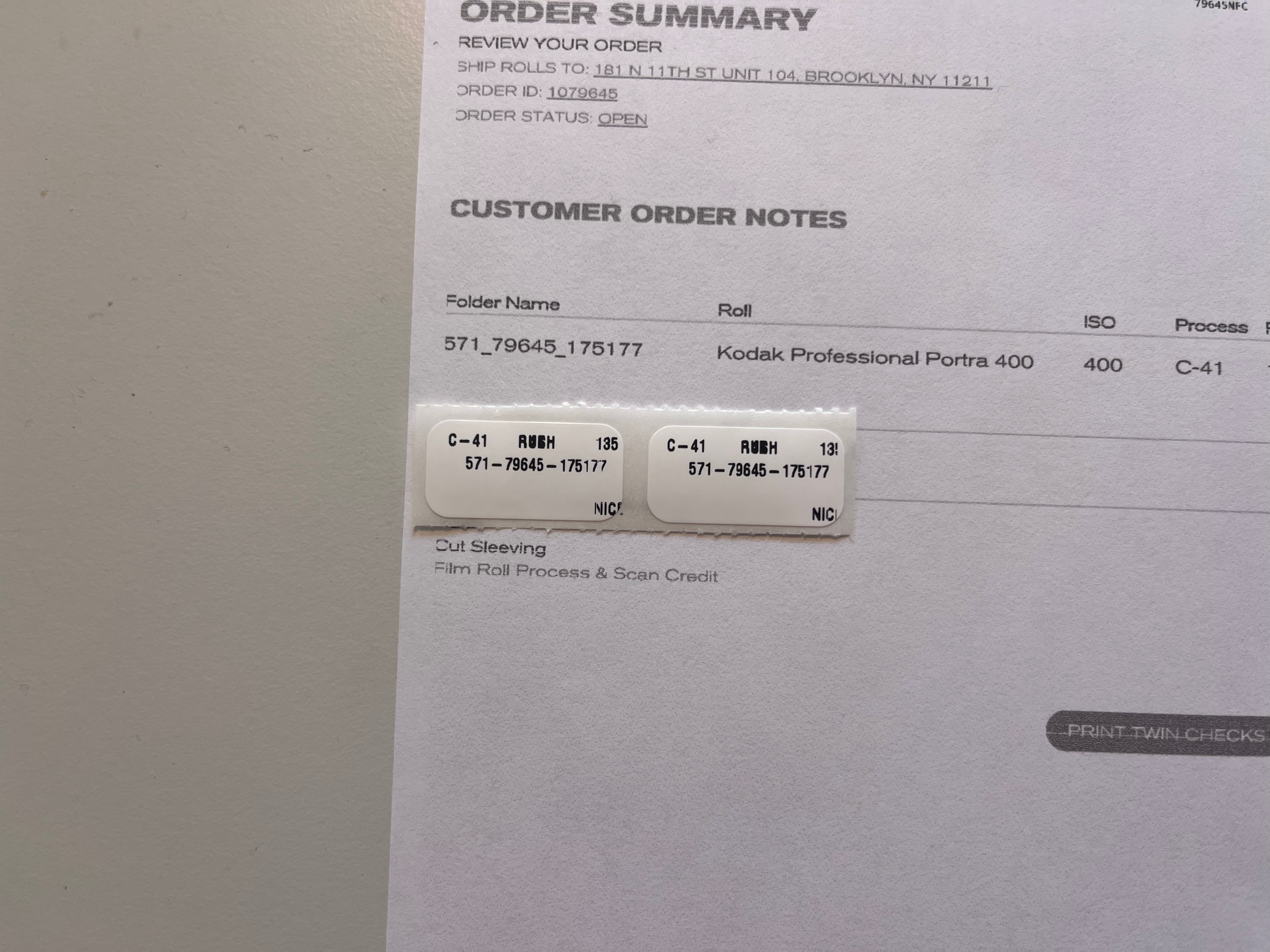

Order Sheets: The Backbone of Our Process
Order sheets are a crucial part of the Nice Film Club process, ensuring every roll of film is handled correctly from start to finish. They contain all the necessary details about your film, helping the in lab team process, track, and deliver each order efficiently. Here’s a detailed breakdown of all the information included on an order sheet and why it matters:
Identification & Tracking
User ID, Order Number, Roll Number
Each order sheet includes three key identifiers to guarantee no roll is misplaced:
User ID: A unique number assigned to you to track your account and orders.
Order Number: A system generated number specific to each individual order. This is the primary identifier used by Nice to locate your orders.
Roll Number: If an order contains multiple rolls, each roll is assigned a unique number to distinguish it within the order.
These identifiers make it easy to match film rolls to the correct order throughout every stage of processing.
Processing Prioritization
Rush
If you opt for rush processing, this will be clearly marked on the order sheet. Rush orders are moved to the front of the queue, ensuring they are developed, scanned, and delivered within one business day.
Tier
Certain membership tiers come with priority processing, meaning your film is placed in a dedicated expedited queue for faster turnaround. For example, Very Nice members have their film automatically prioritized, reducing wait times compared to non member drop offs.
This separate priority queue ensures that high-tier members receive faster service without affecting standard and rush orders, keeping everything efficient and organized.
Customer Information & Sorting
Created By
This field indicates whether the order was:
Placed directly by you online, or
Created in house by a Nice Film Club team member.
This is essential in case an order contains incorrect details. If an issue arises, the team can trace it to the source and correct it quickly.
Film Details for Proper Handling
Film Stock, ISO, Process, and Format
Each roll’s specific details are included to guarantee that they’re developed and scanned correctly:
Film Stock (e.g., Portra 400) – Identifies the brand and type of film.
ISO (e.g., ISO 400) – Does not affect processing but can be a valuable insight when you’re looking back at your uploaded photos to see how your film ISO affected your shots.
Process (e.g., C-41, B&W, E-6, or ECN-2) – Determines the chemical process required for development.
Format (e.g., 35mm, 120) – Makes certain the film is handled with the appropriate scanning and development equipment.
Scan Quality
Scan Quality (2K or 4K)
The order sheet indicates whether the film should be scanned at 2K or 4K resolution which requires manually adjusting output settings prior to scanning your roll. Read more about our scan quality options here
Special Film Processing Instructions
E6/ECN-2 Film Handling
Nice Film Club does not process E-6 (slide film) or ECN-2 (motion picture film) in house. Instead, these film types are sent to a specialized motion picture lab in Atlanta.
The order sheet ensures these film types are separated from the in house batch. If an order contains multiple rolls, it will be split into:
A batch processed in house
A batch shipped to the external lab
This prevents delays and ensures film rolls are sent to the correct locations for processing.
Lab Worker Accountability
Sign Off Sections
To maintain accountability, at the bottom of each order sheet there are designated sections for lab workers to sign off as they complete each step:
Received by – Who checked in the order?
Developed by – Who developed the film?
Scanned by – Who handled the scanning process?
Sleeved by – Who prepared the negatives for storage or return?
If any issues arises during processing, management can refer to the sign off section to trace the problem back to the responsible technician and resolve it efficiently.
Negative Handling Instructions
Negatives Action
Once a roll has been developed and scanned, the order sheet specifies what should be done with the negatives:
Default Policy: If no special instructions are provided, negatives are stored on site for 14 days before being discarded.
Uncut Sleeving: If requested, negatives are placed in protective sleeves but left uncut and placed in a designated area.
Cut Sleeving: If requested, negatives are cut according to their format, put into professional print archival storage sleeves, and archived in your designated folder.
These instructions ensure that your preferences for negative handling are followed accurately and nothing gets misplaced.
Shipping Instructions
Shipping
The order sheet also specifies whether the order needs to be shipped back to you after processing. If shipping is required, the lab team makes sure the order is packaged and sent to the correct address.
Twin Checks: Your Film’s Personal ID Tag
We mentioned that twin checks are packaged along with your film and the order sheet during the intake process. At Nice Film Club, twin checks are the backbone of our workflow, and contain detailed information about your order, making us the only lab in the country with this level of precision. No other lab packs as much vital information into a tracking system this small, ensuring every roll is matched to its order with absolute accuracy. From intake to scanning, twin checks prevent mix-ups, guarantee the correct development process, and ensure your film receives the attention it deserves.
Unlike standard lab tracking, our system provides a one to one connection between each roll and its order, following it through every step of processing. Whether it’s identifying B&W development times, rush orders, or scanning preferences, twin checks keep everything organized and error-free. This level of care is why photographers trust us.
Here’s a breakdown of the Nice twin check system and why it’s essential:
Identification & Tracking
Twin Check Number & Order Matching
Each roll of film receives a twin check number, which is applied in two places:
On the Emulsion of the Film – This label is placed directly onto the film when it is carded before development, guaranteeing it stays with the roll throughout processing. Don’t worry, this does not come near the image area of the film.
On the Order Sheet – A matching twin check label is placed on the order sheet. This allows the roll to be easily tracked at every stage as it moves through the lab.
By keeping this one to one connection, Nice ensures that each physical roll of film is matched to its exact listing on the order sheet. The twin check is placed next to the specific roll it belongs to, making it easy to track and process without mistakes.
Film Processing Information
Processing Type: C-41 vs. Black & White
The twin check indicates the required development process:
C-41 (color negative film)
B&W (black and white film)
For black and white film, the twin check also specifies which processing group the roll belongs to. Since B&W films require different development times, they are broken up into even smaller groups based on processing time. (More details on B&W processing groups will be covered in the next section.)
Film Details for Proper Handling
Format & Film Type
To make certain the film is handled correctly throughout development and scanning, the twin check includes:
Film Format: Specifies whether the roll is 35mm or 120 format.
User Number, Order Number & Roll Number: Ensures that even within a single order, each roll remains uniquely identifiable.
These details help lab technicians sort, process, and scan film correctly, avoiding potential errors.
Processing Prioritization
Rush Processing
If you select rush processing, the twin check will clearly indicate it, making sure the roll moves to the front of the queue.
Scanning Preferences
2K vs. 4K Scanning
The twin check also specifies the desired scanning resolution, same as the order sheet, allowing scanning technicians to sort the film accordingly
2K scans for standard quality
4K scans for high resolution results
Why Twin Checks Matter
Prevents Mix-Ups – Guarantees that each roll is correctly matched to its order throughout the entire process.
Ensures Proper Processing – Provides lab technicians with all necessary details, including processing type, B&W group, and scanning resolution.
Industry Standard Practice – Twin checks are an industry standard practice, ensuring reliability, accuracy, and efficiency. However, the level of detail and information contained in Nice’s twin checks extends far beyond the standard.
Film Development
Once the film is sorted, it moves to the development area of the film lab for processing. This stage involves carefully preparing each roll before it enters the processor, making certain that no frames are exposed to light or damaged.
Film Preparation
35mm Film: Leader Extraction & Carding
The leader of each 35mm roll is carefully extracted using film pickers to prevent accidental exposure.
The tip of the film is trimmed with a film cutter and attached to a specialized leader card using industrial splicing tape for secure processing.
All air bubbles are pressed out ensuring the film remains securely attached during processing.
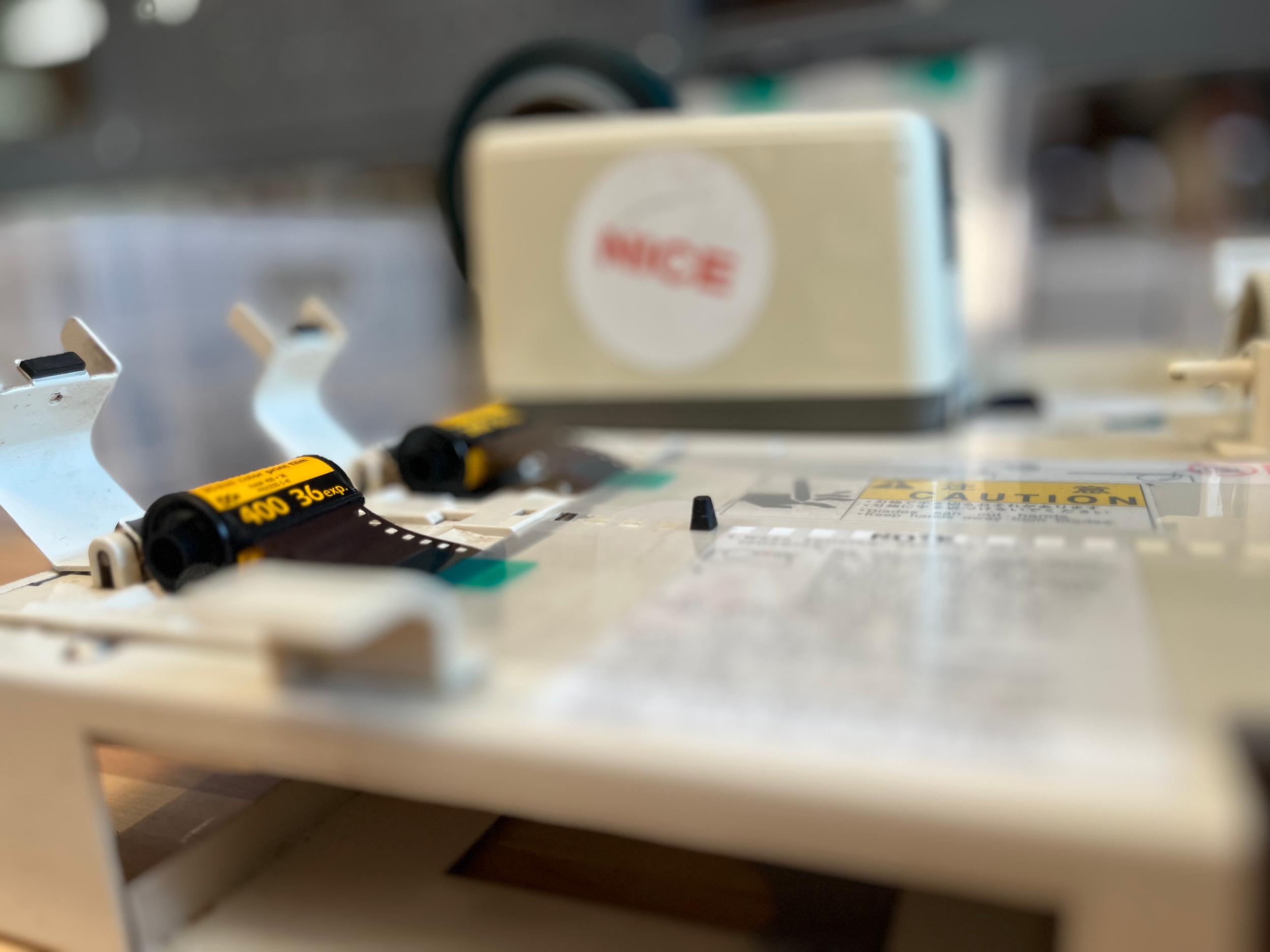

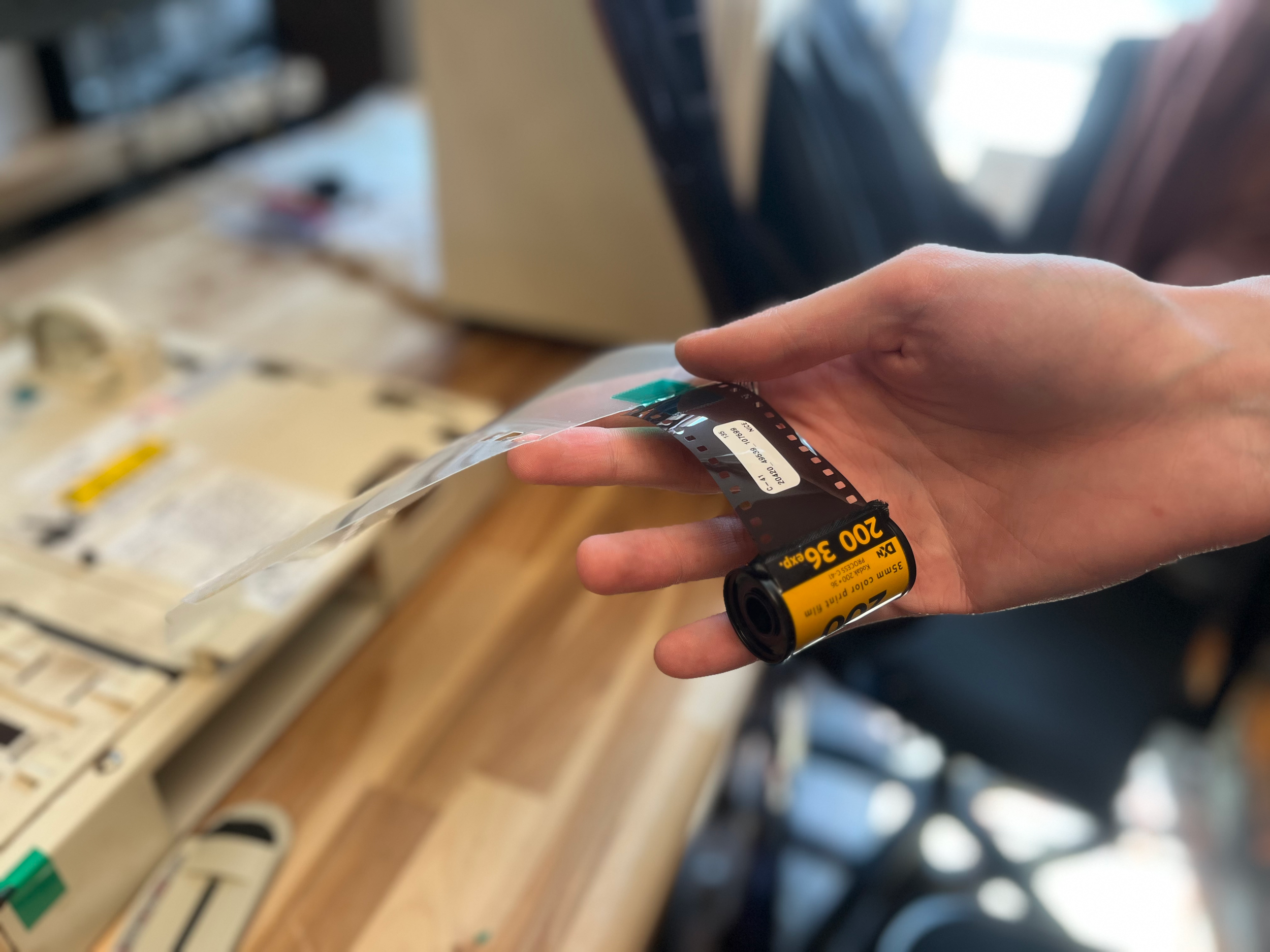
120 Film: Handling & Canister Loading
120 film is handled inside a light sealed dark box to prevent exposure.
The backing paper and adhesive tape securing the film are carefully removed by hand.
The film is placed into a light sealed canister and attached to a leader card, just like 35mm rolls.
Sorting for Development
Color Film (C-41) Processing
Color rolls are arranged in the order they were received and placed in a designated color processing area.
Rolls that require push or pull processing are separated and processed on their own.
Push/pull development is achieved by manually adjusting development time, either speeding up or slowing down the machine to achieve the desired effect.
Because push/pull processing affects machine speed, these rolls are grouped and run at specific times during the day to maximize efficiency.
Black & White Film Processing
B&W rolls are sorted by film stock into time specific subsections based on their development needs. These times are determined by consulting both the individual film stock development guides and the T-Max developer guide.
Unlike color film, black & white film stocks require precise development times, which are calculated based on:
Film type
Constant machine temperature
T-Max developer settings
Example Development Times (Minutes:Seconds):
HP5 and Tri-X → 4:45 minutes
CineStill BWXX → 5:45 minutes
Each B&W subsection is processed separately to ensure the highest level of accuracy and quality control.
Film Processing: Noritsu V50 Roller Transfer Machines
Once prepared, the film is fed into one of our three custom-repurposed Noritsu V50 roller transfer processors:
One machine is dedicated to black & white film.
Two machines are dedicated to color (C-41) film.
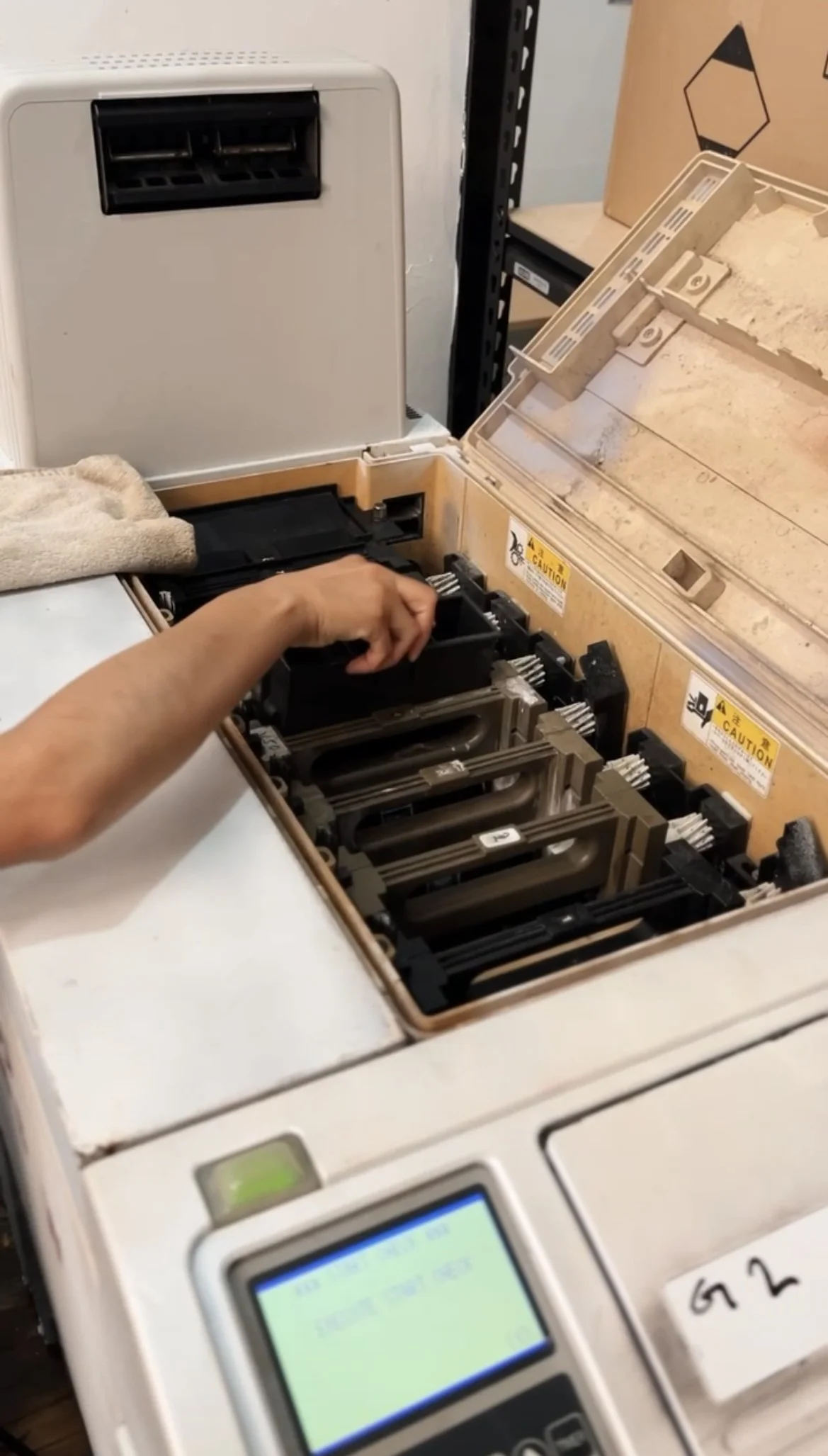
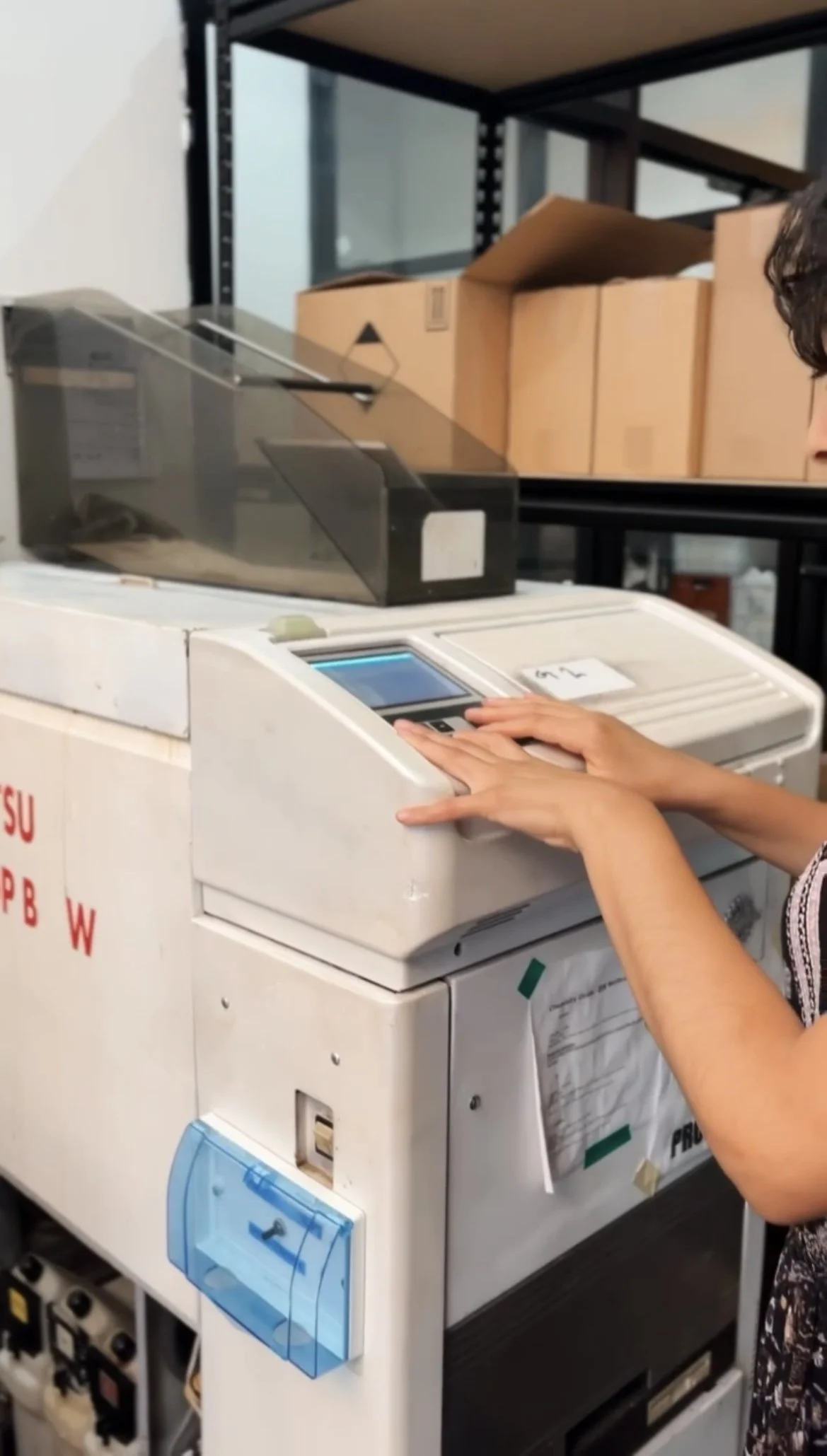
How the Noritsu V50 Works
The Noritsu V50 automates the hand development process by guiding film through each chemical stage:
Developer
Fixer
Bleach (or stop bath)
Stabilizer
Its foam roller transfer system minimizes the risk of scratches or marks on the film, guaranteeing a clean, professional finish.
Why We Use a Roller Transport Machine
Consistency & Quality Control: Eliminates human error and provides trackable, repeatable results.
Optimized Development Times: Adjusted based on film stock and customer preferences.
Faster Turnaround: Speeds up processing while maintaining professional quality results.
While traditional darkroom development may evoke nostalgia, this modernized system prioritizes precision, quality, and efficiency—ensuring exceptional results with faster turnaround times.
Film Scanning
We scan all film using six identical HS-1800 scanners, ensuring consistency and high quality results. Before scanning begins, each machine undergoes a thorough cleaning, calibration, and an air blowing process to remove dust. The film is then carefully loaded into the scanner, starting at frame 1 and ending at frame 36.
You can choose between 2K or 4K resolution, depending on your preferences, and the film will be scanned accordingly. The scanning resolutions are as follows:
35mm (4K): 4492 × 6775 px
35mm (2K): 2000 × 3000 px
6x4.5: 4700 × 3450 px
6x6: 4700 × 4700 px
6x7: 4700 × 5500 px
Once scanning begins, a preview window displays a grid of the images, allowing our technicians to assess the quality and make necessary color or level adjustments. However, our policy is to never make aesthetic judgments or radical alterations unless specifically instructed by you, the photographer. Any preferences or special requests such as "scan flat," "overscan my negatives," or "scan half frames as full frames" should be noted in the "Roll Notes" section of the order.
Our adjustments are focused on making certain that the final images accurately reflect the film stock and the original shooting conditions. We pay close attention to skin tones and potential color shifts, which can occur when scanners attempt to compensate for bold colors in an image. If an image is overexposed or underexposed, we adjust the density to maximize detail while staying true to the original image.
Photos by Sequoyah Images
Once scanning is complete, the files are saved into specific folders corresponding to each scanner and labeled with our custom identifier. Our technicians then perform a final quality check, clicking through a selection of images to identify any unusual markings before transferring the roll to a separate editing folder on our dedicated editing computers.
Editing Your Photos: A Final Round of Quality Control
Our approach to editing aligns with our overall philosophy on scanning—our goal is to make sure that every image meets our high standards while preserving the integrity of your film. We do not make extensive changes but instead focus on refining each scan to eliminate distractions and maintain accuracy.
A technician specializing in editing will primarily remove dust using spot healing, correct orientation, and preform a final quality check to catch any overlooked irregularities or artifacts. If an anomaly appears on a scan, the editor will locate the original negative to determine whether the issue is inherent to the film or a scanning error. Marks imprinted on the negative itself indicate that the issue occurred during shooting. Uniform lines or inconsistencies across multiple frames usually signal a scanning related problem, which can typically be corrected with a rescan.
That said, the most common issues we encounter include camera scratches, hair or debris in the film gate, expired film, heat or water damage, X-ray interference, or mechanical failures. These are all caused by external factors beyond our control. While we cannot always correct these problems in post processing, we make it a priority to provide detailed feedback in the "lab notes" section under your roll, allowing you to understand the likely cause and take preventative steps in the future.
Editing & Pro Scans: A More In Depth Process
While our standard editing process focuses on quality control, Pro Scans involve a more detailed and collaborative workflow that begins in the scanning phase and is further refined during editing.
Pro Scans are our premium scanning service, designed to provide maximum customization and precision. Unlike standard scans, which follow a consistent workflow, Pro Scans allow for tonal and color adjustments tailored to your unique creative vision.
Photos by Sequoyah Images
How Editing Differs for Pro Scans:
Customization from the Start: With Pro Scans, adjustments begin in the scanning phase. You can provide specific instructions, reference images, and stylistic preferences, making certain that scans are aligned with your intended aesthetic.
Fine Tuned Tonal & Color Adjustments: Rather than relying on preset profiles, our technicians meticulously fine-tune the color balance and tonal curves for each roll.
Collaboration & Feedback: You have the ability to review your scans and request refinements after the initial processing. This ensures that the final product matches your expectations.
High Resolution TIFFs for Maximum Flexibility: Pro Scans include 4K TIFF files, providing the highest level of detail and color depth for additional post processing flexibility.
Pro Scans are preferred by professionals who require precise control over their film scans. This process allows for a deeper level of refinement, making it the ideal choice for those seeking ultimate quality and customization.
Regardless of the type of scan you choose, our editing process always prioritizes clarity, accuracy, and preservation of the original film. Our goal is to make sure that your images maintain their authenticity while meeting the highest possible standards.
Archival: Making Sure Your Negatives Stand the Test of Time
Negative Handling & Storage
Once film scans are completed, they are carefully organized based on the next steps for the negatives. Each roll is placed into size specific boxes, paired with its corresponding order sheet, and sorted into designated storage areas based on your requested handling method. This structured system guarantees efficiency, keeps negatives organized, and provides you with multiple options for storing or receiving your film.
Here’s a breakdown of how negatives are categorized and stored after scanning:
Cut Negatives
If you request your negatives to be cut, rolls are cut into strips of six frames and inserted into hole punched plastic archival sleeves designed for long term preservation. These sleeves are then stored in a secure, customer specific, archive folder for one year. This method ensures that negatives remain protected and easily accessible should you request them before the storage period ends.
Uncut Negatives
Negatives requested to remain uncut are carefully placed into sized plastic long sleeves to protect the entire roll. These sleeved rolls are then returned to size-specific boxes and stored in our “uncut rolls” bins, where they will be held for one year before being discarded if no retrieval request is made. This storage option allows you to handle cutting and archiving according to your own preferences.
Shipping Orders
Negatives marked for shipping are immediately transferred to our shipping bins, which are cycled through weekly to create fast and efficient delivery. Our team makes sure that all shipping orders are processed in a timely manner, reducing wait times and guaranteeing that your negatives are returned to you as quickly as possible.
4x6 Print Orders
For rolls that include 4x6 prints, negatives are placed in our printing area, where they are paired with their corresponding order and printed. Once prints are completed, you are notified via email with the option to pick up your order or have it shipped back to you. This ensures a seamless process from scanning to physical prints.
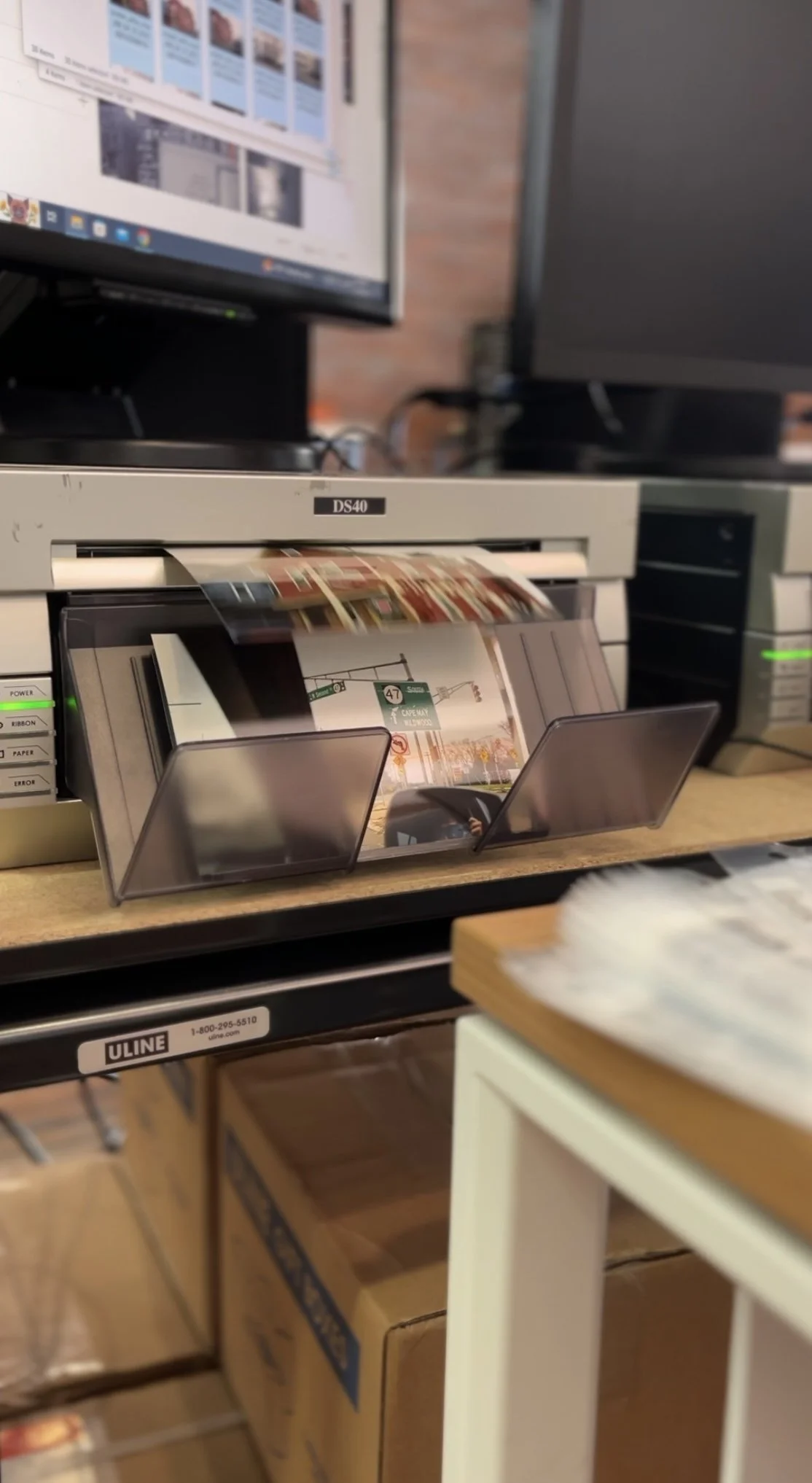
Vendor Orders (Partner Labs & Drop-Off Locations)
Negatives dropped off at partner locations, such as Brooklyn Film Camera, are sorted into vendor bins. These negatives are returned to their respective vendors three times a week, allowing you to pick up your film directly from the original drop off location. This system provides a convenient option if you use third party drop off locations but still want access to our lab's processing and scanning services.
Day Bins: Date Specific Storage
If a roll does not have a specific action requested (cut, uncut, ship, prints, or vendor return), it is placed into a date specific bin inside our lab. These bins are stored in order on our shelving system, allowing us to quickly locate negatives based on the date the scans were uploaded.
This system serves as a tracking method to monitor how long negatives have been held in storage. If a roll is not picked up within 14 business days, it is discarded and marked accordingly in our system.
However, we understand that you may not always be able to retrieve your negatives within the 14 day window. To accommodate this, we offer several automated options to extend storage:
Ship: Negatives can be mailed back to you for a shipping fee.
Cut & Sleeve: Negatives can be cut and archived for the standard cutting fee.
Uncut Sleeving: Negatives can be placed in a protective sleeve and stored in the uncut bin.
Why Our Storage & Handling System Matters
Establishing structured archival and return options from the front end of processing to the final stages guarantees that you have multiple opportunities to retrieve your negatives while also allowing us to manage limited storage space efficiently. This system minimizes errors, ensures timely handling, and helps prevent an overflow of unclaimed negatives, keeping our workflow streamlined and organized.
By providing clear storage policies, multiple retrieval options, and a structured archival system, we make sure that negatives remain accessible and protected while also maintaining a sustainable workflow within our lab.
Uploading and Accessing Your Film Scans
Once your film is uploaded, you will receive a text notification letting you know your photos are ready for viewing. To access them, log into your account and navigate to the "Rolls" section, where your scanned images are hosted.
Photo Hosting & Availability
Members: Your photos remain hosted as long as your membership is active.
Non Members: Your scans are available for 30 days from the upload date.
Viewing Options
In the "Rolls" section, you can explore your images in different formats:
List or Grid View: Choose between a list or grid layout for easier browsing.
Individual Photo View: Clicking on a specific image gives you access to additional features, including:
Submitting Your Work: Submit your photo for a chance to be featured in our newsletters and social media. If selected, you’ll receive 1 free development and scan credit.
Ordering Large Prints: Purchase high quality prints of your favorite images. Both options are easily accessible by clicking the corresponding button at the bottom of each of your photos.
Downloading & High-Resolution Unlocks
Standard Download: Clicking the "Download" button will download your entire roll as individual high resolution 2K images (2000px on the shortest side).
Unlocking 4K 16-Bit Scans (if applicable):
If you paid for the 4K scan add on when submitting your film, you will have the option to unlock 4K 16-bit TIFF files (~100MB each).
Click "Unlock Hi-Res Scans" to access and download these high quality versions, either individually or in bulk.
If you did not purchase the 4K scan upgrade, this option will be unavailible.
Digital Contact Sheet
To enhance your workflow, we offer a digital contact sheet designed to replicate a traditional darkroom contact sheet. This tool allows you to:
View your entire roll in a customizable grid format.
Adjust settings such as resolution, number of frames per roll, and reverse the image order.
Tagging & Organization
To keep your scanned rolls organized, you can:
Add tags with details like location, camera, and lens.
Create custom tags for easier categorization.
Utilize the search function to quickly locate specific rolls based on their tags.
End-to-End Tracking: Unmatched Transparency at Every Step
At Nice Film, we’ve built a fully track-able film processing system designed to give you complete visibility into your roll’s journey. Unlike traditional labs, where film processing occurs behind closed doors, our system enables you to track your roll in real time from the moment it arrives until your scans are ready.
Most labs offer little to no visibility into where your film is in the process. We’ve taken a different approach, developing a system that delivers live updates, precise timestamps, and comprehensive notes at every stage. This means you never have to guess when your scans will be ready or wonder what’s happening with your film.
Internal Event Tracking & Live Updates
Our tracking system goes far beyond just marking a roll as received, developed, or scanned. Internally, we document every step of the process, ensuring full track-ability at every stage.
Each roll progresses through a series of events, all of which are logged in our system with an exact timestamp. These events offer insight not only into key milestones—such as when your roll is developed or scanned—but also into behind-the-scenes actions, such as when twin checks are printed, or when your film is sleeved and archived.
When an event is logged, it exists in a dedicated section within the individual order, allowing us to:
Monitor the entire life cycle of a roll with detailed step by step records.
Identify the exact moment an action occurred using precise timestamps.
Quickly locate and resolve any errors or discrepancies that may arise.
Provide real time updates that are reflected in your "Rolls" section.
Because every step is documented, we can trace a roll’s journey down to the second, ensuring complete accuracy, accountability, and efficiency at all times.
What You See as a Customer
While our lab team has access to detailed event logs and timestamps, what you see is a streamlined version of the tracking system, designed to provide clear, useful updates without overwhelming you with excessive detail.
How to Track Your Roll:
Log into your account and navigate to the "Rolls" section.
There, you’ll see a status timeline that updates in real time as your roll moves through the lab.
Each time a technician logs an event—such as 'Scanned,' 'Developed,' or 'Uploaded'—your status updates immediately.
What You Won’t See:
While you have full visibility into the status of your roll, the detailed backend logs, timestamps, and internal workflow notes remain visible only to our team. This allows us to manage rolls efficiently without cluttering your interface with excessive technical data.
The goal is to provide you with a clear, easy to follow timeline of your roll’s journey while ensuring that every detail is carefully tracked and documented on our end.
Pre Filled & Custom Notes for Detailed Information
A key feature of our event tracking system is the ability to attach detailed notes to each stage of processing. This allows us to provide more context when necessary, ensuring that you receive clear, useful information about your rolls.
When a technician logs an event, they have access to a set of pre filled notes, designed to address the most common questions and concerns related to each stage of the process. These notes provide quick and relevant explanations, helping to eliminate confusion.
For example:
If a roll is marked blank, a pre filled note might clarify whether the roll was completely unexposed, had rebate details but no frames, or had been pre exposed before development.
In addition to pre filled notes, technicians can also add custom notes for further clarification, guarantee that you get specific and detailed insights when needed.
These notes are visible to you within your order, so you’re never left wondering why something happened—you’ll always have a clear, detailed explanation.
Tracking Analog Stations with Barcode Scanning
Not every step of the film process happens in front of a computer, but that doesn’t mean those steps aren’t tracked. Even at stations like development, where a computer isn’t required, we’ve implemented a barcode based tracking system to ensure that every roll remains traceable.
Here’s how it works:
Every order sheet is equipped with a barcode linked to your order in our system.
At the development station, where no computer is present, a barcode scanner is used to log progress.
When a roll reaches development, a technician scans the barcode, instantly marking your roll as "Developed" in our system.
This update is logged internally for our team and in your account under the “Rolls” section.
Additionally, we have set up a live feedback screen at the development station that displays:
Your name and order details
Total number of rolls in the order
Rolls broken down by development type (color, black & white, etc.)
This system ensures that even the most hands on, analog steps of film processing are fully documented, leaving no gaps in the tracking process.
Why This System is Completely Unique
Most film labs depend on manual tracking, unclear processing timelines, and minimal customer visibility. Our end to end tracking system changes that entirely by offering:
Live status updates so you always know where your roll is.
Timestamps for every step, ensuring accuracy and accountability.
Detailed event notes to give you more information when needed.
Barcode based tracking to seamlessly integrate even analog stations into the system.
This level of transparency sets a new standard in film processing, providing unparalleled insight, accuracy, and communication.
Hopefully this blog gave you a detailed look into all aspects of our film photography lab. Sending in film can be nerve-wracking, and labs often provide little transparency about what happens to your rolls. We strive to bridge the gap between our lab and our customers, providing complete transparency and demonstrating why Nice Film Club offers an unmatched film processing and scanning experience.